Digitizing Embroidery Designs: A Comprehensive Guide
Embroidery has been a cherished art form for centuries, evolving from hand-stitched designs to sophisticated machine-embroidered patterns. In today’s digital age, the process of creating embroidery designs has been revolutionized through digitization. Digitizing embroidery designs involves converting artwork into a digital file that embroidery machines can read and stitch onto fabric. This process requires specialized software, technical expertise, and an understanding of embroidery techniques. In this blog, we’ll explore the intricacies of digitizing embroidery designs, its benefits, challenges, and best practices.
What is Embroidery Digitization?
Embroidery digitization is the process of transforming artwork, logos, or designs into a digital format that embroidery machines can interpret. This digital file contains instructions for the machine, such as stitch types, directions, density, and sequence. The goal is to replicate the original design as accurately as possible while ensuring the final embroidered product is durable and visually appealing.
Digitizing is not as simple as scanning an image or converting it into a vector file. It requires careful planning and attention to detail to ensure the design stitches out correctly on the fabric. The digitized file acts as a blueprint for the embroidery machine, guiding it to create the desired pattern.
Why Digitize Embroidery Designs?
1. Precision and Consistency
Digitizing ensures that every stitch is precisely placed, resulting in consistent and high-quality embroidery. This is especially important for businesses that produce large quantities of embroidered items, such as uniforms or promotional merchandise.
2. Customization
Digitization allows for easy customization of designs. You can resize, edit, or modify a digitized file to suit different fabrics, garments, or customer preferences.
3. Efficiency
Once a design is digitized, it can be reused multiple times without losing quality. This saves time and effort compared to manually creating each design.
4. Complexity and Detail
Digitizing enables the creation of intricate and detailed designs that would be difficult or impossible to achieve by hand. This opens up new possibilities for creativity in embroidery.
5. Cost-Effectiveness
While the initial digitizing process may require an investment, it ultimately reduces production costs by minimizing errors and material waste.
The Embroidery Digitization Process
1. Artwork Preparation
The first step is to prepare the artwork or design that will be digitized. This could be a logo, illustration, or any other graphic. The artwork should be clean, high-resolution, and free of unnecessary details that may not translate well into stitches.
2. Choosing the Right Software
Embroidery digitizing software is essential for creating digital files. Popular options include Wilcom, Hatch, Pulse, and Brother PE-Design. These programs allow you to input the artwork and convert it into a stitch file.
3. Setting Parameters
Before digitizing, you need to set parameters such as stitch type, density, underlay, and pull compensation. These settings depend on the fabric type, design complexity, and desired outcome.
· Stitch Types: Common stitch types include satin stitches (for outlines and text), fill stitches (for large areas), and running stitches (for fine details).
· Density: This refers to the number of stitches per inch. Higher density is used for thicker fabrics, while lower density works better for delicate materials.
· Underlay: Underlay stitches provide a foundation for the design, stabilizing the fabric and preventing distortion.
· Pull Compensation: This accounts for the fabric’s tendency to pull or stretch during embroidery, ensuring the design remains aligned.
4. Digitizing the Design
Using the software, you trace the artwork and assign stitch types and directions to each element. This step requires a good understanding of how stitches interact with fabric and how different stitch types affect the final result.
5. Testing and Editing
Once the design is digitized, it’s tested on a sample fabric to check for any issues, such as gaps, misalignment, or thread breaks. Based on the test results, adjustments are made to the digital file.
6. Saving the File
The final digitized file is saved in a format compatible with the embroidery machine, such as .DST, .PES, or .EXP. This file is then loaded onto the machine for production.
Challenges in Digitizing Embroidery Designs
While digitizing offers numerous benefits, it also comes with its own set of challenges:
1. Complex Designs
Highly detailed or intricate designs can be difficult to digitize, as they may require a large number of stitches and careful planning to avoid thread breaks or fabric damage.
2. Fabric Compatibility
Different fabrics behave differently during embroidery. For example, stretchy fabrics like knits require special considerations to prevent distortion, while thick fabrics like denim may need adjustments in stitch density.
3. Color Blending
Achieving smooth color transitions in embroidery can be challenging, as the medium relies on discrete stitches rather than continuous tones.
4. Time-Consuming Process
Digitizing is a time-intensive process, especially for complex designs. It requires patience, skill, and attention to detail.
5. Learning Curve
Mastering embroidery digitizing software and techniques takes time and practice. Beginners may struggle with creating high-quality designs initially.
Best Practices for Digitizing Embroidery Designs
To achieve the best results, follow these best practices:
1. Start with High-Quality Artwork
The quality of the final embroidery depends on the quality of the original artwork. Use clean, high-resolution images with clear outlines and minimal complexity.
2. Understand Fabric Properties
Different fabrics require different digitizing approaches. Consider factors like stretch, thickness, and texture when setting parameters.
3. Use Appropriate Stitch Types
Choose stitch types that complement the design and fabric. For example, satin stitches work well for text and borders, while fill stitches are better for large areas.
4. Optimize Stitch Density
Avoid excessive stitch density, as it can make the design stiff and prone to thread breaks. Similarly, too little density can result in gaps and poor coverage.
5. Test and Refine
Always test the digitized design on a sample fabric before full production. Make necessary adjustments to ensure the final product meets your expectations.
6. Keep Learning
Embroidery digitizing is a skill that improves with practice. Stay updated on new techniques, software updates, and industry trends.
Applications of Digitized Embroidery Designs
Digitized embroidery designs have a wide range of applications across various industries:
1. Fashion and Apparel
From custom t-shirts to haute couture, digitized embroidery adds a unique touch to clothing and accessories.
2. Corporate Branding
Businesses use digitized logos on uniforms, promotional items, and corporate gifts to enhance brand visibility.
3. Home Décor
Embroidered designs are used to create personalized home décor items like pillows, curtains, and table linens.
4. Sports and Team Gear
Sports teams and organizations use digitized embroidery for jerseys, caps, and other gear.
5. Personalized Gifts
Digitized embroidery is popular for creating personalized gifts, such as monogrammed towels, bags, and keepsakes.
The Future of Embroidery Digitization
As technology continues to advance, the future of embroidery digitization looks promising. Innovations in software, machines, and materials are making the process faster, more accurate, and more accessible. Some trends to watch include:
· Automated Digitizing: AI-powered tools are emerging that can automate parts of the digitizing process, reducing the time and effort required.
· 3D Embroidery: Techniques for creating three-dimensional embroidery designs are gaining popularity, adding depth and texture to patterns.
· Eco-Friendly Practices: Sustainable materials and processes are becoming a focus in the embroidery industry, aligning with global environmental goals.
Conclusion
Digitizing embroidery designs is a blend of art and technology, requiring creativity, technical skill, and attention to detail. While the process can be challenging, the results are well worth the effort. Whether you’re a business owner, designer, or hobbyist, mastering embroidery digitization opens up a world of possibilities for creating stunning, customized designs. By following best practices and staying informed about industry trends, you can elevate your embroidery projects to new heights. Embrace the digital revolution and unlock the full potential of this timeless craft!
What's Your Reaction?
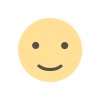
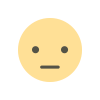




